News
Aerodynamic optimization of the eSAIL®: advancing Wind-Assisted Propulsion
Published
01 October 2024
-
In February 2023, bound4blue participated in the Wind Propulsion Conference organized by RINA, presenting a research paper on the exceptional aerodynamic performance of the eSAIL, which significantly surpasses that of the Turbovoile.
-
The bound4blue team has optimized the aerodynamic performance of its wind-assisted propulsion system, the eSAIL®, through CFD simulations and wind tunnel testing, achieving a 20% improvement in the lift-to-power ratio.
-
With validated tools, bound4blue is now fine-tuning the eSAIL®’s autonomous control for real-world applications, maximizing fuel savings and emissions reduction for each installation.
bound4blue continues to push the boundaries of maritime innovation with the latest advancements in its wind-assisted propulsion system, the eSAIL®. Developed to reduce fuel consumption and emissions, the eSAIL® utilizes suction sail technology, originally pioneered by the Cousteau Foundation’s TurboVoile. This paper highlights how bound4blue’s aerodynamics team has fine-tuned its tools to further optimize the eSAIL® for real-world applications, making significant strides toward the green energy transition in shipping.
With the TADC in place, bound4blue expects “accelerated technical due diligence processes” with customers, paving the way for a simpler system roll-out. This will help shipowners, removing the burden of individual quality validation, speeding up access to eSAIL® benefits including reduced fuel consumption and emissions, lower OPEX, and simplified compliance with the most stringent regulatory demands.
The role of CFD in eSAIL® development
The foundation of the eSAIL® optimization process lies in Computational Fluid Dynamics (CFD) simulations. Initially, these simulations were calibrated against experimental TurboVoile data, the only available experimental dataset for suction sails. This provided a reliable starting point for bound4blue to validate its tools and proceed with further design optimization.
➡️ Download the full paper & presentation ⬅️
Exploring the design space
Once CFD tools were validated, bound4blue embarked on a comprehensive exploration of the suction sail’s design space. This included 2D parametric studies to identify the most promising geometries, followed by more intricate 3D simulations. These simulations examined various factors that influence performance, such as fan characteristics, winglet effects, suction area porosity, and local disturbances in the suction area.
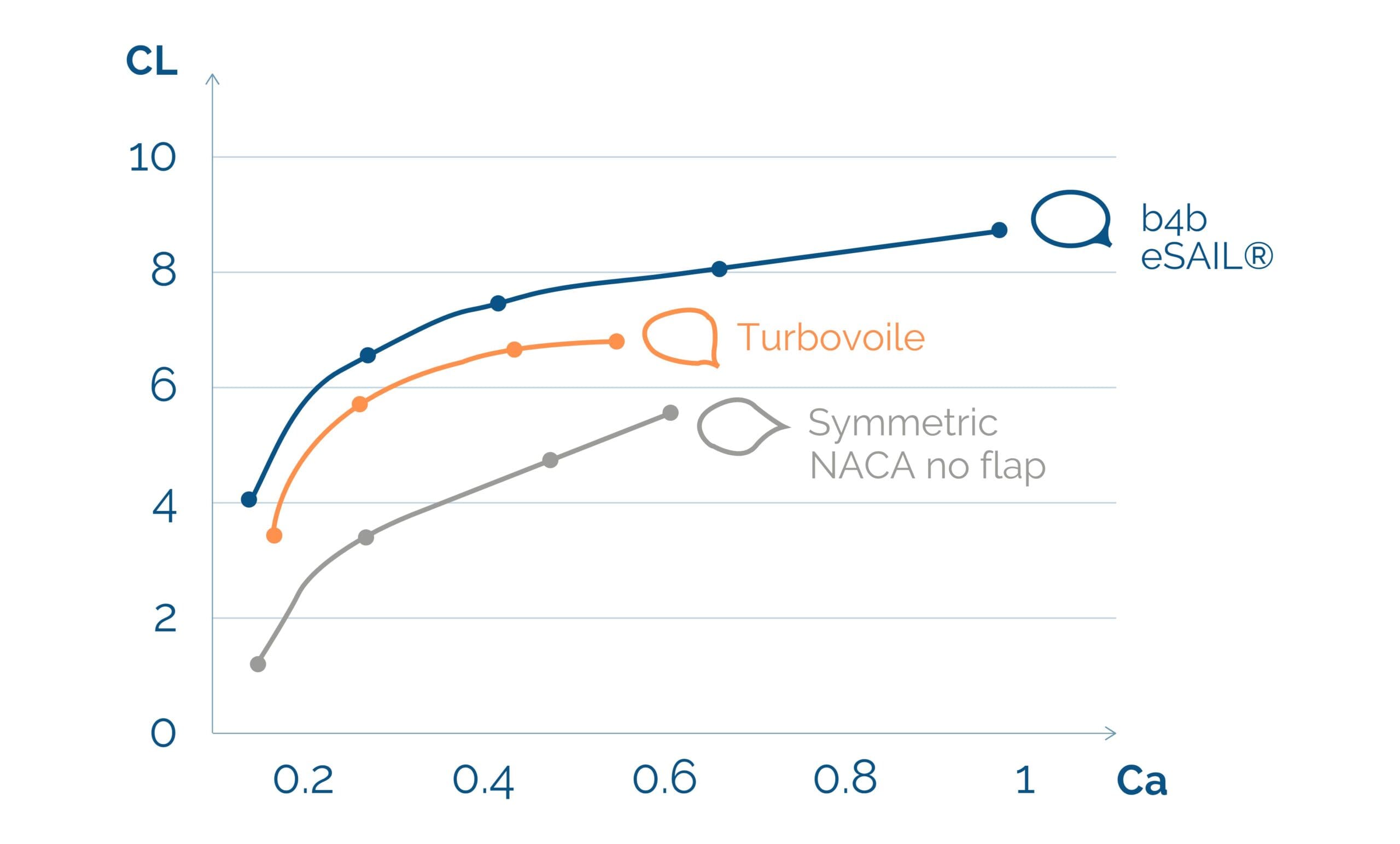
Wind tunnel validation
Before fully trusting the CFD results, a wind tunnel campaign was conducted to validate the findings. The goals were twofold: first, to confirm the CFD results, and second, to further refine the calibration of bound4blue’s tools. The wind tunnel tests showed excellent correlation in pressure and force data, giving the team high confidence in its ability to predict real-world performance.
Efficiency improvements
The culmination of this research was a 20% improvement in the lift-to-power ratio compared to TurboVoile, with a maximum lift coefficient of 8.3. These improvements make the eSAIL® a more efficient solution for wind-assisted propulsion, allowing for greater fuel savings and emissions reductions.
Real-world applications
With a solid foundation of validated CFD simulations, bound4blue has now moved toward simulating more complex, real-world conditions. These include factors such as the atmospheric boundary layer, sail-to-sail interaction, and ship-to-sail interaction. By incorporating real ship data, bound4blue can fine-tune the eSAIL®’s autonomous control algorithm for each installation, ensuring maximum fuel and emissions savings.
A future of sustainable shipping
These advancements in eSAIL® technology demonstrate bound4blue’s commitment to leading the maritime industry’s transition to sustainable energy solutions. By optimizing aerodynamics, improving efficiency, and incorporating real-world data, bound4blue is helping shipowners and operators significantly reduce their environmental impact while maintaining operational efficiency.
About the author
Alberto Llopis Pascual holds the current position of Lead Aerodynamics Engineer at bound4blue. He is responsible for aerodynamic development of bound4blue’s technology, both numerical and experimental. Alberto holds a PhD in Aerospace Engineering in the field of experimental aerodynamics (University of Manchester, 2017). Previously, he spent 6 years working with University of Manchester, BAE Systems and a NATO task group researching and developing fluidic control effectors for aircraft, designing, and building the first aircraft to fully integrate and demonstrate this technology. Later, he also spent 2 years carrying out aerodynamic design of medical delivery drones.